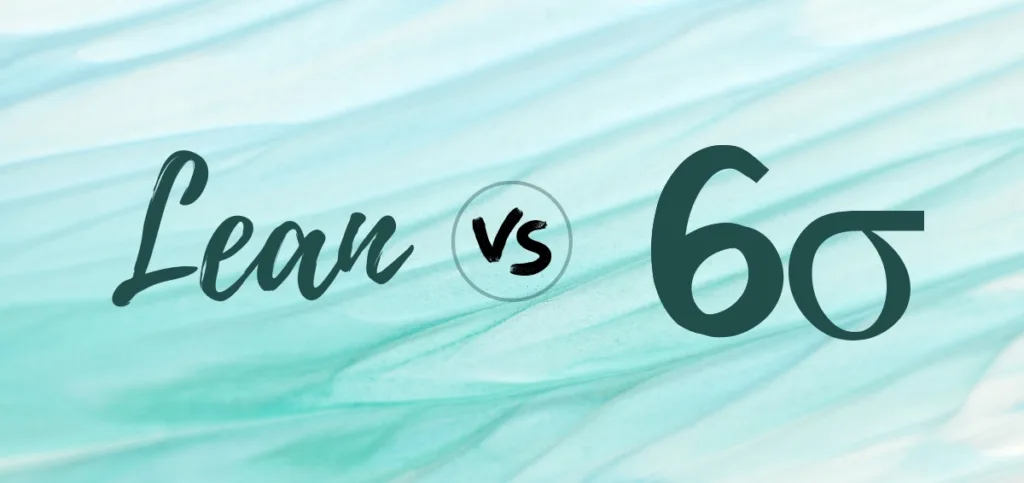
Lean and Six Sigma are two of the most well-known approaches to optimizing business efficiency. Almost all project management professionals are aware of these terms, and few use them interchangeably, as both serve the same purpose: enhancing business processes. Numerous organizations have used one or both of these methodologies to achieve process excellence. Understanding their distinctions is critical if you, too, want to accomplish the same. In this post, we will lay down the key differences between Lean and Six Sigma.
Read Also: Fundamentals of Marketing: Everything You Need to Know
Understanding the Lean Methodology
The best way to understand the lean methodology is through the example of food. Lean foods, such as lean meat, are considered good because they do not have excess fat, which can prove harmful to the body. Similarly, lean methodology is aimed at cutting the surplus from your project. This, in turn, keeps it in a better shape. In other words, the lean approach focuses on making processes more efficient by eliminating wasteful or unnecessary tasks. This approach facilitates a process of continuous incremental judgment, fast-tracking product delivery through resource optimization. It paves the way for efficient workforce work.
Understanding the Six Sigma Approach
Six Sigma is a methodology that revolves around enhancing the quality of a product. All the practices in this approach are aimed at finding and reducing the defects in a product in the shortest amount of time. The Six Sigma approach encompasses the following: Outlining the issue – gathering the relevant data to better understand the cause(s) of the issue – Assessing the information gathered – Using the assessment to resolve the issue – And establishing procedures to maintain the improvement.
Must Read: Why is Foresight Not Getting Traction with Business?
How Does Lean Differ From Six Sigma?
Lean and Six Sigma approaches differ on various fronts. Let’s explore their key differences.
Lean vs Six Sigma – The Essence
The essence of Lean is completely different from Six Sigma. The Lean approach, at its core, is a mindset rather than a specific action. Lean is a set of principles that facilitate ongoing process improvements. It, in turn, reduces waste, keeping the project in a better shape. Six Sigma is more methodical. It comprises a series of defined steps that address and resolve problems. The approach is more structured, and every individual has specific tasks and responsibilities. Everyone’s work contributes to the end goal of eliminating defects from the product. The approach is ideal for a hierarchical organization.
Lean vs Six Sigma – The Origins
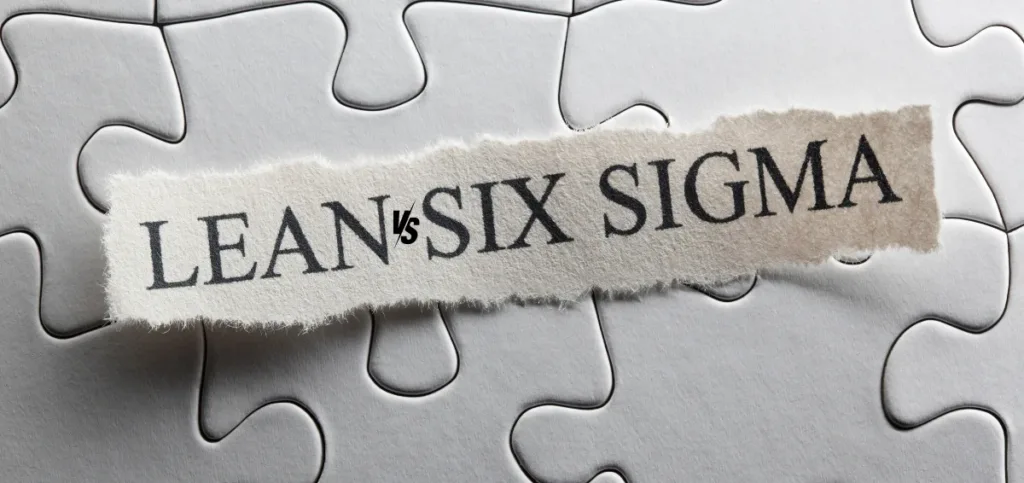
The origins of Lean go as far back as the 1450s. The shipbuilders at the Venetian Arsenal could successfully move ships through their production line through sequencing and standardizing. They accomplished this huge task in just an hour! The standardization of the process flow led to the enhancement of quality, efficiency, and safety. The Lean approach continued to evolve and found a beautiful expression in the 20th century. It was when Eiji Toyoda, the nephew of Sakichi Toyoda, the founder of the Toyoda Automatic Loom Works, became aware that the mass production system wasn’t suitable for the Japanese market due to its small size. So, he created a new means of production, which involved right-sizing machines for the actual volume. They introduced self-monitoring machines to make products fast, high quality, and cost-effective.
The name Six Sigma comes from the bell curve in statistics. Here, one Sigma denotes a single standard deviation from the mean. A process showing Six Sigma is understood to have a very low defect rate. The approach took off when General Electric applied it in its processes to save costs while enhancing the quality and eliminating waste. This led many other organizations to employ it and achieve similar results. Today, the approach is mostly used to enhance workflow processes, which have a compounding positive influence on the organization.
Lean vs Six Sigma – Core Principles
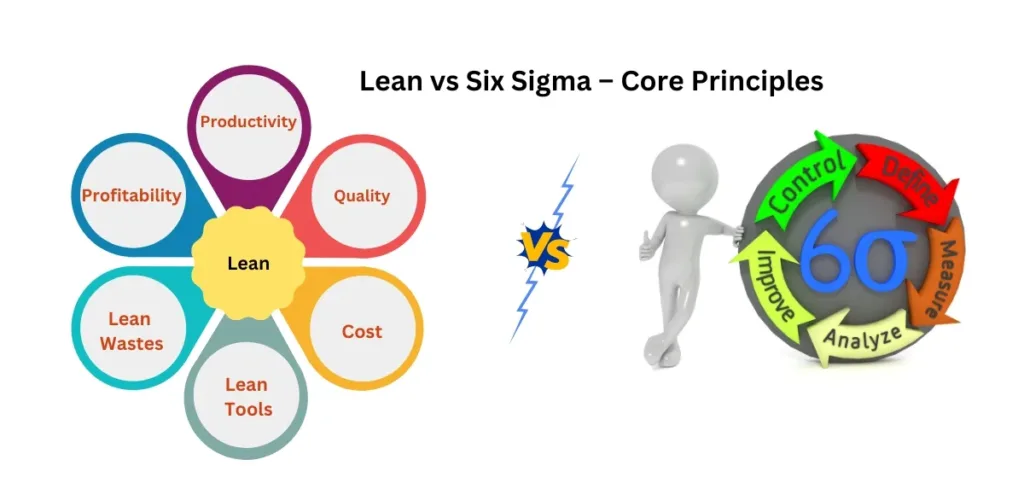
There are five core principles of Lean. These include:
- Identifying the value that the customer gets from a product.
- Visualizing the path of the value to the customer.
- Creating a smooth flow of receiving the order to the final delivery.
- Creating a pull system. This means beginning new work only when there is a demand for it.
- Constantly optimizing the process by improving the activities that create the most value for the end customer.
There are seven principles of the Six Sigma approach. These include:
- Focus on the needs of the customer when creating a process.
- Making the process smoother for uninterrupted execution.
- Reducing waste in a process.
- Eliminating process variations to optimize it and maintain its uniformity.
- Improving a systematic process through process management techniques.
- Equipping every person involved in the process with the right training and tools to perform their jobs well.
- Observing the occurrence of the process, documenting it, and using this observation to find out areas of improvement.
Read Also: 8 Sales Closing Techniques to Finalize Every Deal
Lean vs Six Sigma – Ideal Use Cases
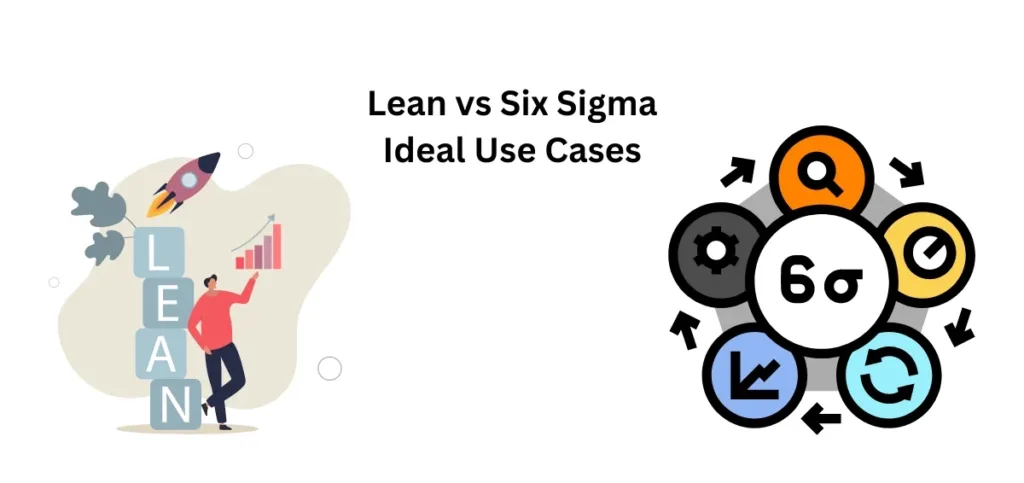
The Lean approach can be employed in various types of organizations. It benefits every business desiring rapid, incremental improvements. The approach is generally ideal for small to medium-sized businesses with limited resources.
On the other hand, the Six Sigma approach is suitable for organizations with projects with quantifiable outcomes. Often, large-sized businesses implement this methodology to achieve tangible growth outcomes. These businesses need greater investment in resources, and so the Lean approach, focusing on waste elimination, doesn’t suit them.
Lean vs Six Sigma – Tools and Applications
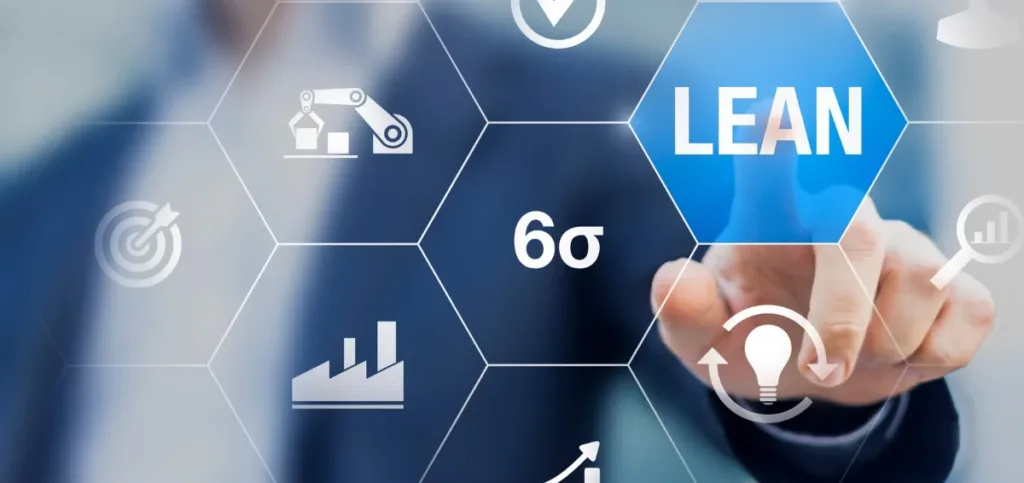
In their approach, Lean and Six Sigma utilize different tools, each tailored for specific applications.
Lean tools and their applications
- Bottleneck analysis is a lean tool that refers to analyzing the stages that are causing inefficiency in processes.
- The Just-In-Time (JIT) tool minimizes waste due to over-production.
- Value Stream Mapping, or VSM, helps visualize processes, leading to a greater understanding of them.
- Error Proofing maintains and sustains improvements.
- The Overall Equipment Effectiveness or the OEE helps in understanding the usefulness of a process to the outcome.
Six Sigma tools and their applications
- The Voice of the Customer (VOC) tool gathers customers’ opinions and needs, which are then analyzed to gather key insights.
- Value Stream Mapping refers to visualizing the process to identify and resolve bottlenecks.
- The Pareto Chart shows how frequently the causes of an issue occur.
- The process Capability approach finds the process’s existing capabilities to check whether it fulfills the customer’s requirements.
- Regression Analysis is a statistical technique used to find the relationship between different variables. This relationship is key to identifying inefficiencies.
Final Thoughts
Lean and Six Sigma are both used to optimize business processes. However, they differ pronouncedly in their nature and application. Lean revolves around waste elimination, while Six Sigma is more concerned with minimizing defects. A clear understanding of this approach will help you choose the best one for your project and achieve the desired success.